In today’s world, gelcoat and fibreglass are integral components found in countless products across major industries like marine, automotive, and construction.
But how many of us truly understand the difference between gelcoat and fibreglass? Having this knowledge is crucial for making informed decisions as consumers and professionals.
At their core, gelcoat and fibreglass are the key players that combine to form strong, lightweight composite materials. Gelcoat provides a smooth, protective outer layer while fibreglass reinforces the structure with its woven strength.
Together, they create tough yet aesthetically-pleasing products tailored to withstand harsh conditions.
Whether you’re a boat owner buffing your hull, a car enthusiast admiring a glossy paint job, or a builder constructing weather-resistant siding, you’re interacting with these remarkable materials.
Taking the time to truly comprehend gelcoat and fibreglass can help you make smarter choices and gain a deeper appreciation for the engineering marvels around you.
Keep an open mind as we move forward. Some characteristics of gelcoat and fibreglass may surprise you and challenge preconceived notions. But arming yourself with facts allows you to navigate the world of composites confidently.
Table of Contents
What is Gelcoat?
Let’s start with gelcoat – that glossy, protective outer layer you see on so many fibreglass products. At its simplest, a gelcoat is a specialized resin coating applied to the mould before the fibreglass laminate is formed.
Its key purpose? Creating an attractive surface finish while guarding against the elements.
But gelcoats are more than just a pretty face. They’re a precisely blended mix of rigid thermoset polymers like polyesters or vinyl esters, pigments for colour, fillers for thickness, and additives to enhance properties like UV resistance.
This robust formula yields a tough, durable coating able to maintain its lustre for years.
Thanks to its versatility, you’ll find gelcoat hard at work across many sectors:
- Marine: Watercraft like boats, personal watercrafts, and kayaks rely on gelcoated hulls and decks to stay sleek and sea-worthy.
- Automotive: The smooth, colourful finishes on car bodies, truck caps, and automotive panels? Often gelcoat at play.
- Construction: Architects leverage gelcoat’s aesthetic and resilience for exterior cladding, shower stalls, countertops, and more.
- Transportation: Everything from RVs to semi-truck trailer bodies get the gelcoat treatment for visual appeal and longevity.
So while gelcoat may just seem like a cosmetic layer, it’s truly an intelligently-designed surface champion protecting the underlying fibreglass composite.
What is Fibreglass?

If gelcoat is the sleek outer surface, fibreglass is the hidden muscle providing strength and structure to composite products. Fibreglass itself is a reinforced plastic made up of fine glass fibres woven together and bonded by a resin material like polyester.
But how does this powerful material take shape? The manufacturing process is quite fascinating.
Glass fibres are first extruded at incredibly high temperatures, allowing them to maintain their strength while becoming endlessly flexible strands.
These fibres are then woven into sheets or fabric, combined with liquid resin, and cured to create the solid fibreglass laminate.
Once solidified, fibreglass exhibits some truly extraordinary properties:
- Strength: Those interwoven glass fibres give fibreglass incredible tensile strength able to reinforce and bear heavy loads.
- Lightweight: Despite its toughness, the material’s makeup keeps its weight low compared to metals.
- Corrosion Resistance: Fibreglass won’t rust, rot, or degrade even in harsh environments like salt water.
- Insulation: With low thermal and electrical conductivity, it makes an effective insulator.
- Flexibility: While solid, fibreglass can bend and conform to curves without compromising integrity.
This unique blend of power and versatility is why fibreglass forms the backbone of so many dependable products we use daily without a second thought.
Key Differences Between Gelcoat and Fibreglass
A. Material Composition
- Gelcoat: A gelcoat is a specialized resin-rich coating primarily made from thermoset polymers like polyesters or vinyl esters. It contains pigments for colour, fillers for thickness, and additives to enhance properties like UV resistance and weather protection. Gelcoats have a thick, viscous liquid consistency that allows them to be applied as a smooth, glossy surface layer.
- Fibreglass: On the other hand, fibreglass is a true composite material consisting of extremely fine strands of glass fibre reinforcement that are woven together and bonded by a separate polymer resin matrix like polyester, vinyl ester or epoxy resins. The glass fibres provide exceptional tensile strength while the resin allows the material to solidify into its final rigid shape.
B. Function
- Gelcoat: The primary function of a gelcoat is to form an attractive yet highly durable outer surface finish that protects the underlying fibreglass composite from environmental factors like UV radiation, moisture, and physical impacts. It provides aesthetic appeal with its glossy, colourful appearance.
- Fibreglass: Fibreglass serves as the main load-bearing structural reinforcement component. Its tightly woven glass fibres give fibreglass products remarkable strength-to-weight ratios, allowing them to bear heavy loads and impacts without deforming or fracturing.
C. Application
- Gelcoat: In composite manufacturing, the gelcoat is applied as the final surface layer over the cured fibreglass laminate. It is sprayed or rolled into the mould first before the fibreglass layers are added, creating a protective and visually appealing “skin.”
- Fibreglass: The fibreglass laminate forms the central core and backbone of the composite product. Multiple layers of woven fibreglass are laid into the mould along with the resin system which binds everything together as it cures, giving the product its strength and shape.
D. Properties
- Gelcoat: While formulated to be highly resistant, gelcoats can be susceptible to chipping, cracking, chalking and fading over time from UV exposure, chemical attack or mechanical abrasion. Their outermost surface takes the brunt of environmental stresses.
- Fibreglass: Known for its excellent strength properties, fibreglass laminates also exhibit impressive flexural strength, heat resistance, moisture resistance, and corrosion resistance thanks to the impervious nature of the glass fibres. The composite construction makes them incredibly durable.
Common Applications
A. Gelcoat:
- Marine Industry: Take a walk down any marina and you’ll see gelcoat’s handiwork everywhere – from the sleek, glossy hulls of powerboats and sailboats to jet skis, kayaks and paddle boards. Those layers of vibrant gelcoat not only make them look shipshape, but protect the fibreglass underneath from corrosion, UV radiation, and sea spray.
- Automotive Industry: Next time you’re admiring a new car’s deep, shimmering paint job, look closer – you may just be appreciating expertly applied gelcoat! Many automotive manufacturers use gelcoated fibreglass body panels and components for their strength, low weight, and eye-catching looks.
- Construction Industry: Architects and builders turn to gelcoat composites for both visual appeal and resilience. You’ll find gelcoated fibreglass cladding home exteriors, forming sleek countertops, and providing durable surfaces for bathroom units, shower enclosures and even decorative planters.
B. Fibreglass:
- Marine Industry: If gelcoat is the environmental armor, fibreglass is the ultra-tough hull and structural skeleton holding those boats and watercrafts together through pounding waves and strikes. Its corrosion-resistance makes it ideal for the harsh marine environment.
- Automotive Industry: Automobile manufacturers leverage fibreglass laminates to construct remarkably lightweight yet robust vehicle bodies, roof components, trunk lids and other parts that require high strength but minimal weight for efficiency.
- Aerospace Industry: When strength and weight are paramount, aerospace engineers turn to fibreglass composites for aircraft components like fuselages, wings, and rotor blades. Its flexibility allows these parts to withstand intense forces while remaining aerodynamically sound.
Whether providing aesthetic lustre, structural brawn, or a strategic blend of both, it’s clear that gelcoat and fibreglass are the indispensable driving forces behind resilient and eye-catching products across industries. Their unique strengths allow product designers to push the limits of form and function.
Maintenance and Care
Gelcoat: While prized for its durability, a gelcoat surface still requires some routine pampering to retain that fresh, glossy appearance year after year. Periodic polishing with a specialized compound helps restore oxidized or dull coatings to their vibrant former selves.
And just like our own skin needs protection from harmful UV rays, gelcoats should be treated with a sealant or wax designed to block UV radiation and prevent chalking or fading over time. Neglecting this can cause even the richest color to turn ashy and lackluster.
It’s also crucial to promptly repair any chips, cracks or crazing in the gelcoat. These flaws create opportunities for moisture intrusion that can lead to delamination or osmotic blistering of the underlying fibreglass laminate – essentially compromising the entire composite structure.
Fibreglass: In contrast, that hard-working fibreglass laminate beneath the gelcoat finish is remarkably low-maintenance by nature. The tightly woven glass fibres are impervious to moisture, corrosion, and most chemicals.
However, periodic cleaning is still recommended to prevent build-up of grime, salt, soot or other contaminants that can gradually wear on the surface over years of exposure. A simple rinse with mild soap and water is usually sufficient.
Additionally, it’s wise to regularly inspect accessible fibreglass components for any signs of physical damage like cracks, stress fractures or delamination between layers.
These areas create potential failure points that may need to be reinforced or repaired by a professional to preserve structural integrity.
While fibreglass is undoubtedly one tough customer, a little routine care and vigilance goes a long way in ensuring both the glossy gelcoat topcoat and brawny fibreglass underbody can continue performing their complementary roles for decades to come.
Conclusion
Throughout this guide, we’ve examined the distinct worlds of gelcoat and fibreglass that harmoniously unite to create composite products prized for their strength, durability and aesthetic appeal across industries.
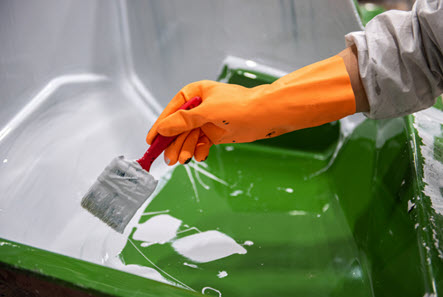
While both play critical roles, their differences are fundamental:
- Gelcoat is a specialized resin coating providing a smooth, glossy outer layer to protect the fibreglass laminate beneath.
- Fibreglass is the mighty reinforcing core made of woven glass fibres embedded in resin, giving the product its structural integrity.
One focuses on surface resilience and beautification, the other on fortifying the underlying skeleton and form.
Developing this understanding is invaluable whether you’re a professional product designer, manufacturer or just an educated consumer. It allows you to make informed choices about speccing the right composite system for the job – balancing durability needs and maintenance expectations with appearance and cost criteria.
If issues like blistering, delamination or cracking arise down the road, knowing the root cause is crucial for executing proper repairs that address the gelcoat, fibreglass or both components. Improper fixes can undermine the product’s longevity.
What’s most remarkable is just how ubiquitous and invaluable gelcoat and fibreglass composites have become as engineering marvels underpinning our daily lives.
We benefit from their versatility whether zipping over water in a fibreglass speedboat, gripping the fibreglass handles of our workout equipment, or admiring the sleek gelcoated exterior of a luxurious automobile.
By understanding their symbiotic differences and strengths, we can appreciate the thoughtful design and ingenuity allowing these materials to enhance both form and function in countless applications.
Gelcoat and fibreglass are the ultimate power couple enabling countless modes of work, transportation and recreation while surrounding us in durable beauty.
FAQs
Is gelcoat the same as fiberglass?
No, gelcoat and fiberglass are distinct materials. Gelcoat is a resin-rich coating applied over fiberglass composites, while fiberglass refers to the actual reinforced plastic made of glass fibers and resin.
How do I know if my boat has gel coat?
If your boat has a smooth, glossy colored surface finish, it almost certainly has a gelcoat layer providing that protective cosmetic finish over the fiberglass laminate beneath.
Can you fiberglass on top of gelcoat?
Yes, you can apply additional layers of fiberglass over an existing gelcoat surface after properly preparing and roughening the gelcoat to promote adhesion.
Is gelcoat just resin?
No, while resin is a key ingredient, gelcoat is a specialized coating containing pigments, fillers, and additives that allow it to provide both cosmetic and protective properties.
Do I need gelcoat over fiberglass?
For most fiberglass composite products, a gelcoat layer is highly recommended to protect the structural fiberglass from environmental damage like UV radiation.
Can I use resin instead of gelcoat?
Using just resin alone instead of a true gelcoat is not recommended, as it lacks the specific formulation needed to create a durable cosmetic finish.
What are the two types of gelcoat?
The two main types are polyester gelcoats and vinyl ester gelcoats, with vinyl esters offering superior chemical and blister resistance.
What does gelcoat not stick to?
Gelcoat can have adhesion issues with certain materials like polyethylene, silicones, and contaminated surfaces, so proper preparation is required.
How waterproof is gelcoat?
A properly applied gelcoat forms a water-resistant barrier, but can develop cracks or crazing over time that lets moisture penetrate if not maintained.
Do you need to sand fiberglass before gelcoat?
Yes, the fiberglass surface needs to be roughened by sanding to allow the gelcoat to mechanically adhere properly.
How long does a gelcoat last on a fiberglass boat?
With proper care and maintenance, quality gelcoats can last 10-15 years before requiring refinishing or repairs on boat hulls and components.
What is the purpose of gelcoat on fiberglass?
Gelcoat serves two key purposes – providing an attractive coloured surface finish, and protecting the underlying fiberglass laminate from UV damage and weathering.